In addition to metallurgical elements, water chemistry has a strong influence on the corrosion course of in zirconium alloys. The control of water chemistry as required in several reactor methods embrace appropriate additions of lithium hydroxide, boric acid, hydrogen/deuterium, oxygen, iron, and zinc. In PWRs, boric acid is added to the coolant water for reactivity control. The pH of the coolant is adjusted by addition of lithium hydroxide which renders the coolant barely alkaline, so as to cut back the corrosion rates of structural supplies (stainless steels and Inconels) within the major warmth transport circuit and thereby inhibit deposition of corrosion merchandise on the gas cladding. Radiolysis of water produces oxidizing species which boosts oxidation rate of zirconium alloys in the radiation surroundings .
is produced and the chance of an enormous secondary hydriding failure is elevated. In response to this unexpected consequence, a number of fixes have been launched.
The constants a and b are basic properties of the fabric and could be determined from commonplace laboratory experiments on contemporary fuel. In explosive welding, a compression force created by detonation of explosives is used to affix overlapping metal sheets. The joining components are organized towards one another at an angle of 1–15°, depending on the material and methodology, and are prepared with a layer of explosive on the highest. After ignition the joining areas are moved towards one another at excessive velocity.
Zry production methods now provide much better management of gaseous impurities than early fabrication technology, so the unique purpose for adding tin is moot. Since tin is a substitutional impurity, its operate is to increase the power of Zry over that of pure zirconium. 1.5% tin, and the balance being iron, nickel, and chromium.
In one, a second inside-floor liner of strange Zry is extruded on the sponge zirconium liner in order to restore corrosion resistance. In other modifications, the sponge zirconium is alloyed with iron or tin to enhance oxidation resistance with out affecting the softness that provides immunity from PCI. Standard Zry is sufficiently hard to be susceptible to emphasize-corrosion cracking (SCC) when the pellet–cladding gap closes and the swelling gas generates substantial tensile hoop stresses within the cladding. In the presence of an aggressive fission product (iodine is most often cited), a brittle crack can be initiated and penetrate the cladding wall.
With it, we process particular person parts in addition to collection elements, inside as well as outer contours, new and used elements. Cladding in development is materials utilized over one other to offer a skin or layer and used to supply a level of thermal insulation and weather resistance, and to enhance the appearance of buildings. Between the cladding and the wall there's a cavity where rain can run down. Laser cladding with the help of power-primarily based or wire-formed filler materials can be utilized for restore work, the application of wear and corrosion safety and the manufacturing of 3D components (additive manufacturing).
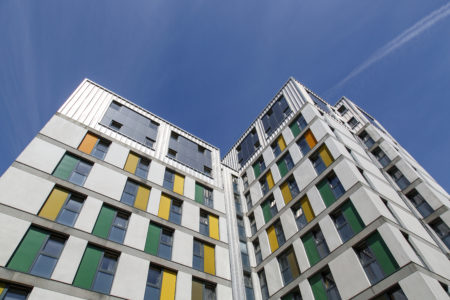
Metal parts

The graphite layer provides lubrication to minimize the mechanical interactions, and acts as a barrier towards the migration of dangerous species to stressed areas of gas tubes. The unique purpose of tin in Zry was to mitigate the loss of corrosion resistance caused by pickup of impurity nitrogen during fabrication of the alloy.
Dissolved oxygen in PHWR coolant is controlled between 10–50 ppb and it has been noticed that corrosion in each zircaloy-2 and Zr-2.5 Nb pressure tubes rises to an exceptionally high value at high oxygen concentrations. The BWR coolant normally contains a higher stage of oxygen, sometimes 200–four hundred ppb.
This is a main cladding failure that admits steam into the rod with the accompanying potential for a more critical secondary failure because of hydriding. The combination of circumstances (prone steel, tensile stress, and chemical enhancer) that produces the primary defect is termed pellet–cladding interaction (PCI). scale that grows around them throughout in-reactor operation. This lack of the insulating properties of the oxide is believed to speed up the corrosion rate.
The constants a and b are basic properties of the material and can be decided from standard laboratory experiments on recent fuel. In explosive welding, a compression drive created by detonation of explosives is used to join overlapping steel sheets. The joining elements are arranged towards one another at an angle of 1–15°, relying on the fabric and methodology, and are prepared with a layer of explosive on the top. After ignition the becoming a member of areas are moved in opposition to each other at excessive velocity.
These approaches have encountered problems, together with porosity of the cladding, uneven cladding thickness, dilution of the cladding alloy due to the large heat enter required, and distortion of the workpiece by the excessive heat enter. Laser cladding has decreased these problems and produced cladding layers with good uniformity, good dimensional management, and minimal dilution of the cladding alloy. offers a survey of a cladding tools. If the incoming strips must be heated in order to decrease the strength of materials, this has to be carried out as close as attainable to the rolling gap and in a protective environment in order to keep away from oxidation of the cleaned and roughened surfaces. We provide excessive-quality ornamental products that improve any house and interior.
Applications for Surface linked here Treatment
Today, Zircaloy-2 and Zircaloy-4 are extensively used. Phase transformation of Zirconia is, nonetheless, of great concern.
Long-time period, in-reactor, oxidation, and hydrogen choose up conduct of zircaloy-2 and Zr-2.5Â Nb stress tubes, displaying parabolic after which accelerated linear oxidation and hydrogen pickup kinetics in zircaloy-2. A low and uniform rate of corrosion and hydrogen choose up is seen in the in Zr-2.5Â Nb alloy. Differential swelling between cladding, wrapper tube, and spacing system (spacer wire or grids) can induce extra stresses and deformations on these elements and/or generate coolant move perturbations in the bundle. These phenomena have been studied and have particularly proven that wires or grid supplies should be chosen and specified to be able to minimize differential swelling.
Enhance the curb enchantment of your home with B&Q cladding. All of our timber is responsibly sourced forest pleasant timber.
The resulting cladding layer was properly bonded, and the blades exhibited improved fatigue traits compared with blades fashioned by the conventional silver brazing course of. laser beam. The alloy was overlaid on the steel as a powder layer 2.5 mm thick. After melting and bonding by the laser, the alloy layer was 1.5 mm thick and had very little dilution from the steel. The ensuing floor had wonderful put on resistance.
The complete melting of the filler ends in a dense layer with optimum adhesion to the substrate. The most typical application is for the wear and tear safety, e.g. of instruments, but also corrosion safety or high temperature resistance can be specifically improved. Common exhausting alloys based on cobalt, nickel and iron are used with and with out the addition of exhausting materials. But additionally particularly adapted materials can be applied.
Our huge range of products contains PVC wall panels, outdoors wall cladding, waterproof flooring as an alternative to laminate or LVT, waterproof bathe and toilet panels and far more. These embody cladding, small steel pins coupled with a ceramic mass, half-pipes and SiC tiles, as well as numerous forms of coatings, together with thermal spray coatings. Its characteristic characteristic is the sash bar down the middle of the window and black (just like RAL 9005) metallic cladding coverings on the window and flashing which matches traditional buildings. The Independent Expert Advisory Panel also advised the department to determine a research project to test and improve the proof out there on the behaviour of a variety of non-ACM materials used in cladding systems when subjected to fire.
Alloying elements, particularly tin, niobium, and iron, current in the α-stable resolution strongly influence both the kinetics and the mechanism of oxide growth in zirconium alloys. ions from the surroundings to the response front at the metallic/oxide boundary.
The compromise between these competing calls for has produced wall thicknesses of ∼0.9mm in BWRs and ∼0.7mm in PWRs. Laser cladding usually involves covering a comparatively inexpensive substrate material with a more expensive alloy that will increase the resistance of the part to wear or corrosion.
Zry manufacturing strategies now provide much better management of gaseous impurities than early fabrication know-how, so the unique purpose for including tin is moot. Since tin is a substitutional impurity, its operate is to extend the energy of Zry over that of pure zirconium. 1.5% tin, and the steadiness being iron, nickel, and chromium.
The thickness of the cladding might vary between 0.1 and 30 mm and the detonation velocity is between 1200 and 7000 ms −1 . The high plate hits the underside plate with a speed of a hundred–one thousand ms −1 , and pressures are in the range of 10 to one hundred kbar. Under certain situations a superheated layer of material forms within the contact space. The joint is then caused by a deformation-induced melting bathtub.
laser. The clad substrates confirmed improved oxidation traits compared with the original alloy. Conventional methods for cladding have employed tungsten-inert gas welding, plasma spraying, and flame spraying.
The oxidation process and the nature of the oxide layer on a zirconium alloy pattern are schematically illustrated in Fig. 6 . Cladding is an outer layer of either vertical or horizontal material, used to improve the looks, thermal insulation and the weather resistance of a constructing. Our cladding is on the market in quite a lot of sizes, forms of timber and surface finishes.

First Known Use of cladding

Cladding allows the majority of the part to be made with inexpensive materials, while providing the surface with desirable properties associated with the costlier cladding materials. Laser cladding has resulted in surfaces with superb finish, good homogeneity, and really low porosity. Common materials used for cladding embrace carbides, iron-based mostly alloys, nickel base alloys, and cobalt base alloys. Laser cladding is a process in which a steel coating is applied onto the floor of an element utilizing a laser as the heat source.
Dissolved oxygen in PHWR coolant is managed between 10–50 ppb and it has been observed that corrosion in both zircaloy-2 and Zr-2.5 Nb stress tubes rises to an exceptionally high worth at excessive oxygen concentrations. The BWR coolant usually contains a better stage of oxygen, typically 200–four hundred ppb.
As the oxide layer grows, the compressive stress on the outer layer of oxide just isn't sustained and consequently the tetragonal part turns into unstable and transforms into the monoclinic part. Such a transformation causes the formation of a nice interconnected porosity in the oxide film which allows the oxidizing water to come in contact with the metallic surface. With the event of an equilibrium pore and crack construction in the oxide layer, the oxidation price successfully turns into linear, a attribute feature of the submit-transition oxidation conduct.
Depending on the supplies to be bonded, cleaning and roughening are best carried out by brushing, grinding, or scraping using a specifically designed cutter with needles. A suction removing unit is used to evacuate carefully any materials waste so as to avoid bonding flaws on account of poor adhesion. Laser cladding permits us to apply metallic layers for wear and corrosion protection with great precision. In addition, it can be used to repair and modify elements.
The melt layer is kind of thin; for instance, when cladding an aluminum alloy it's about 0.5–4μm (Kreye 1985, 1997 ). The dilution of the molten zones leads to plane or corrugated interfaces. During mechanical decladding, the gasoline assemblies are chopped and the fuel core is leached with nitric acid, forsaking the undissolved cladding materials for disposal as a stable waste.